Die Projektpartner
Das Forschungsprojekt steht in Zusammenarbeit mit der neugeründeten Professur für Mineral Construction Materials an der TU München und ist vom BMBF geförderten. Weitere Partner kommen aus der Forschung und der Industrie - darunter IBU-tec, Lithonplus, Kraft Curing Systems, Heidelberg Materials und die Friedrich-Alexander-Universität Erlangen-Nürnberg.
Reduzierter Kalksteineinsatz zur CO2-Reduktion
Der Ansatz des Projektes in der Entwicklung des Verfahrens besteht in einer ganzheitlichen Reduktionsstrategie für die Betonherstellung, Zemente unter Verwendung von recyceltem Betonabbruch herzustellen und somit die Verwendung von Kalkstein zu reduzieren, die für einen Teil der Emissionen verantwortlich ist. Dauerhaft gebunden wird das CO2 in Beton durch die Karbonatisierungshärtung. Praktisch erprobt wird der Einsatz des hergestellten Zements dann in der Produktion von Betonpflastersteinen. Im Gegensatz zur Herstellung herkömmlicher Zementklinker wird somit die CO2-Emission während des Brennprozesses gemindert.
Vom Labor zum Scale-up im Drehrohrofen
Zur Herstellung von belitischem, kalkarmen Klinker führte der erste Schritt bei IBU-tec ins Labor. Untersucht wurden verschiedene Rohmehlmischungen bezüglich ihrer Behandlungstemperatur und Verweilzeit in der Karbonatisierungshärtung. Dafür konnten wir unseren dynamischen Laborbrennofen nutzen – ein eigens konstruierter Ofen, der es ermöglicht, die Probe mit einem Aufheiz- und Abkühlprogramm zu behandeln, welches den Bedingungen in einer großtechnischen Anlage nahekommt. Anschließend erfolgte die physikalische und chemische Charakterisierung zur Auswertung der verschiedenen Edukte. Die Variationen in der Zusammensetzung der Rohmehlmischungen machten eine detaillierte Untersuchung im Labormaßstab nötig, um aus den Versuchsergebnissen die Prozessparameter für spätere Pilotversuche in einem Drehrohrofen im Technikumsmaßstab festlegen zu können.
Dieser Drehrohrofen für den ersten Schritt des Scale-ups ist eine unserer Technikumsanlagen, hat eine beheizbare Länge von ca. sieben Metern und diente zur Herstellung von Mustermengen, die im gemeinsamen Projektfortschritt für verschiedene Prüfschritte in der Evaluation benötigt werden. Nach einer ausführlichen Charakterisierung wurden die vielversprechenden Rezepturen ermittelt und mit ihnen erneut in derselben Technikumsanlage Klinkerproben produziert und abermals ausgewertet.
Ergebnisse unserer Versuche
Die Erkenntnis: Der Ansatz funktioniert! Erfolgreich haben wir gemeinsam mit unseren Projektpartnern einen CO2-reduzierten Klinker entwickelt und im Technikumsmaßstab hergestellt. Der nächste Schritt ist nun das weitere Scale-up in eine Anlage im größeren Pilotmaßstab. Wir wollen Pilotmengen herstellen, die die Erprobung des entwickelten Klinkers in realen Endprodukten möglich machen, wofür wir die Rezepturen mit dem größten Karbonatisierungspotenzial ausgewählt haben. Unsere Produktionsanlage ist ein direkt beheizter Drehrohrofen mit einer Länge von ca. zwölf Metern, die Produktion wird im Herbst beginnen und vorerst 10 Tonnen betragen. Das dann hergestellte Material soll bereits in der Herstellung von Betonpflastersteinen als Endprodukt zum Einsatz kommen.
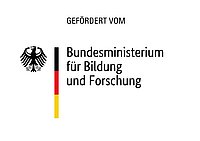
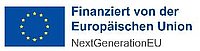